Project Arthrex
- Customer demand -
Densify storage on picking shelves to better respond to its new "chaotic" inventory management.
- The Provost solution -
With Provost's advice, and thanks to the modularity of PROSPACE + shelving, the number of picking locations was doubled in one year (from 1900 to 4000), without changing the organization of the building.
- 3 400 m2
- 4,000 product locations
- 2,700 products
Optimizing medical device logistics
Arthrex manufactures and distributes medical devices in over 100 countries worldwide. It is a major player in the orthopedic and medical device markets. At its French logistics site in Nord (59), Arthrex manages the inbound and outbound flows of over 2,700 products, supplying its hospital and clinic customers throughout France.
"Our 3,400 m2 site has seen its activity intensify in recent years. The overall growth of our company, combined with a change in our ERP*, has led to an increase in stock volumes and the number of separate storage locations," explains Jérôme SIMON, logistics coordinator at Arthrex. "We needed to increase the density of our picking shelves to better respond to our new "chaotic" inventory management.
Solutions implemented
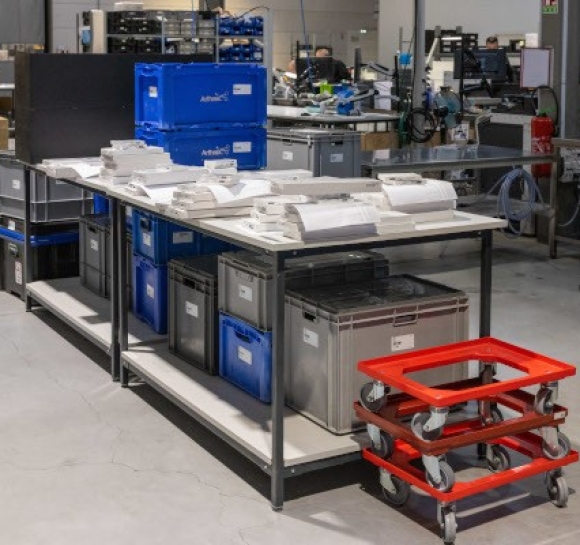
From reception to dispatch, a layout adapted to each workflow
"For the past 6 years, our logistics site has been growing steadily. Thanks to the breadth of its offer, Provost has provided us with solutions tailored to the equipment of each of our cells."
- In the receiving and control areas, we equipped Arthrex with workstations and plastic bins.
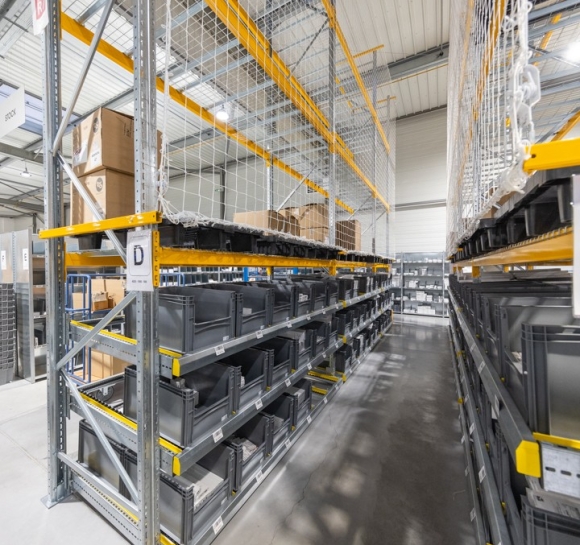
Pallet racking for packaging and overstock storage
In the storage areas, Provost equipped Arthrex with Propal 3 pallet racks for storing their packaging and overstock.
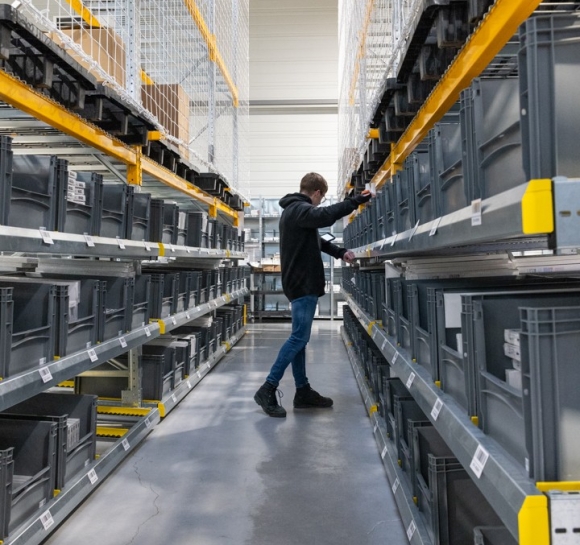
Lightweight shelving for order-picking cells
For their order-picking cells, we equipped Arthrex with Prospace + fixed light shelving, and dynamic shelving picking levels under the pallet racks, as well as order-picking carts.
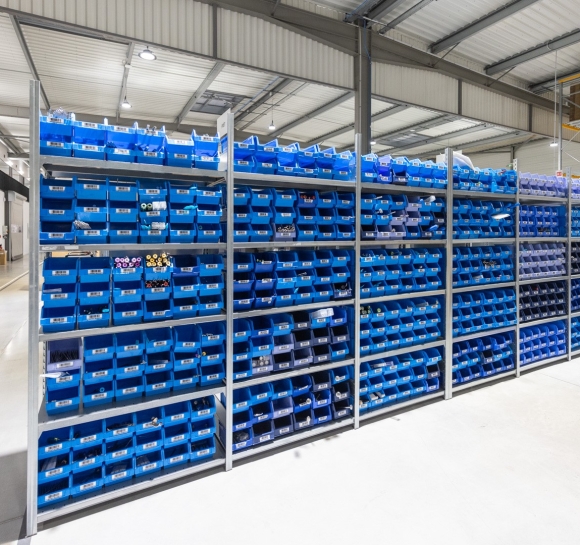
Medium-heavy shelving and bins
Arthrex also lends equipment to its customers: cases of ready-to-use medical devices. To store these cases, we equipped Arthrex with Prorack+ medium-heavy shelving
For the storage of small parts, we were able to provide a plastic bin solution.
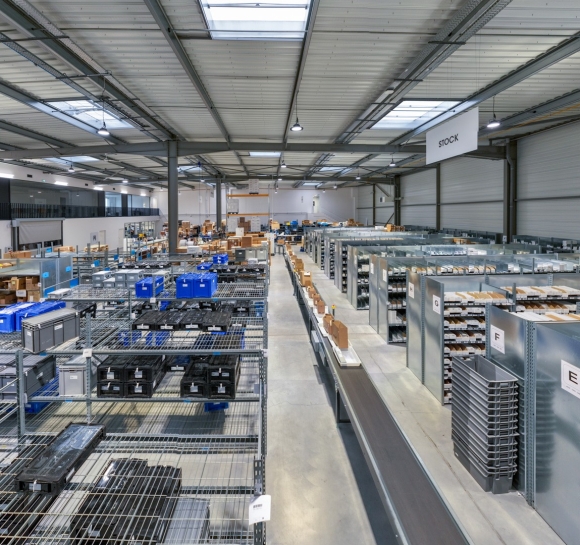
Customer benefits
Order preparation is made easier: 400 parcels are dispatched every day.
"What made the difference on this project? Our ability to offer equipment for all stages of logistics. Arthrex uses our worktops in the receiving or packing areas, our fixed or dynamic shelving for storing the various parts, our picking carts for order preparation, or even bins and rolling bases to facilitate handling. "
Grégoire, technical sales representative.
Do you have a project in mind?
Our team of 80 sales representatives and 20 technicians in France can help you with all your needs.
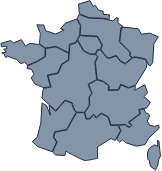