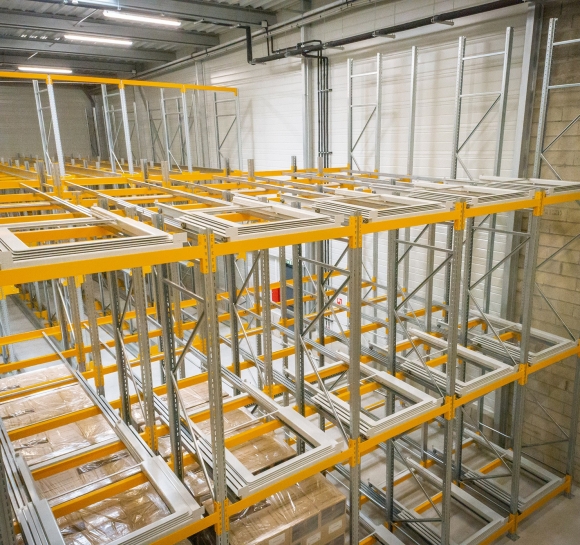
Dynamic storage - optimize your flows
Storage and order picking are crucial to the efficient management of logistics flows. That's why we offer you 3 innovative dynamic storage systems to optimize these operations: dynamic roller racking (Prodyn+), dynamic pallet racking and pushback accumulation storage. If you're looking to improve the efficiency of your warehouse, explore these solutions today.
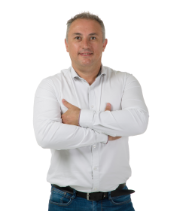
Optimize your logistics with our dynamic storage solutions
At Provost, we understand the importance of storage and order picking for the efficient management of logistics flows. That's why we offer three innovative dynamic storage systems: dynamic roller racking (Prodyn+), dynamic pallet racking and pushback accumulation storage.
Prodyn+ is perfect for picking, ensuring logical product rotation using the FIFO (First In - First Out) principle.
The pallet flow storage system is ideal for regularly rotating, high-volume goods, ensuring permanent availability of products on the front of the rack.
Finally, our pushback storage solution optimizes your order picking by adopting the LIFO (Last in - First out) principle.
These systems save time and space, facilitate the work of pickers and ensure optimal inventory management. However, it's crucial to consider several criteria when choosing the dynamic storage system best suited to your needs, such as the nature of your products, your requirements in terms of storage capacity, handling efficiency, safety and compatibility with your current handling equipment. Discover Provost's dynamic storage solutions today.
Lightweight dynamic shelving for picking

Benefits
Time saving

Solution
Tailor-made
Dynamic shelving on rollers (Prodyn+) is a solution that facilitates handling and speeds up order picking. Thanks to the FIFO (First In - First Out) principle, it ensures a logical rotation of products and prevents aging. This system saves up to 70% in order-picking time, and up to 30% in space by eliminating aisles. Separate storage and retrieval zones facilitate the work of order-pickers, and products are lowered by gravity onto roller tracks, reducing internal handling time and optimizing your order-picking process. +.
I discover the solutionDynamic storage rack for pallets

Manufacturing
Provost

Benefits
Time saving
The dynamic gravity pallet storage system is designed to store pallets of various sizes and stacked loads. We can offer you customized solutions for dynamic gravity pallet racking or through-roller pallet racking.
Ideal for regularly rotating, high-volume goods with a low number of SKUs, this system guarantees permanent availability of products on the front of the rack. In double-sided approach, it provides a FIFO (first in - first out) system, while in double-sided or opposite-sided supply, a LIFO (last in - first out) system is obtained.
Dynamic pallet racking offers significant time savings in order picking, reducing picking distances by up to 70%, and space savings of around 30% thanks to the elimination of aisles. This solution is ideal for optimizing your logistics flows and handling operations.
I discover the solutionPushback dynamic rack storage

Manufacturing
Provost

Benefits
Time saving
Pushback storage is a solution to boost your order picking. Suitable for medium-rotation goods, it enables LIFO (Last in - First out) storage and saves time during order picking.
Compared with Drive-in storage, Pushback storage offers more flexible inventory management, with 1 reference equivalent to 1 slot. It can accommodate up to 9 pallets deep and loads of up to 1,200 kg.
The nesting table principle enables pallets to be moved by pushing on rails, with pallets descending by gravity. Loading and unloading take place on the same side of the storage system, without the need for the forklift to enter the system.
The PROVOST Pushback carrier is equipped with a fill indicator, making it easy for operators to locate the available spaces. The Pushback racking can also be supplied with through rollers for use in refrigerated warehouses.
I discover the solutionDynamic shelving and accumulation storage systems
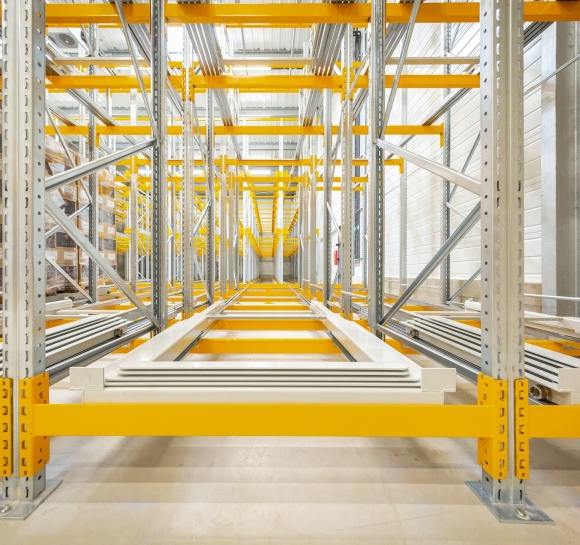
Discover our Pushback accumulation storage solution in this video. This innovative system considerably increases your storage capacity and facilitates your handling operations, saving you precious time.
Pushback features a unique accumulation system with mobile frames sliding on a metal rail, with each pallet resting on its own mobile cart. Pallets are moved simply by pushing, making handling easier and more efficient.
Particularly suited to medium-rotation goods, our push-back carrier applies the LIFO (last in - first out) storage principle.
Compared with drive-in warehousing, pushback offers far more flexible inventory management, as each product reference corresponds to a single location. In other words, 1 part number = 1 location, unlike the Drive-in system where 1 part number = 1 aisle.
The Pushback system can store up to 9 pallets deep and loads of up to 1,200 kg. What's more, this solution eliminates the need for the operator to enter the storage facility, reducing the risk of collision or damage.
Don't miss this opportunity to optimize your warehouse with our Pushback accumulation storage solution
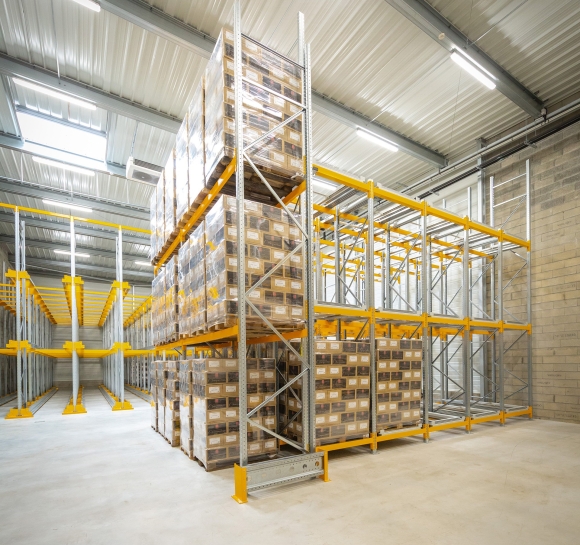
Setting up a dynamic storage system
Our three dynamic storage systems optimize storage and order-picking operations, saving time and space, and making pickers' work easier. Opt now for these innovative solutions and maximize your profitability.
Criteria to consider
To select the dynamic storage system best suited to your business, consider the following criteria:
Step 1: Product analysis
Assess the turnover, volume and number of SKUs of your products. For example, pallet flow racking is ideal for goods with regular turnover, while pushback storage is suitable for products with medium turnover.
Step 2: Storage capacity and available space
Estimate the surface area of your warehouse and the storage capacity required. Also consider the flexibility of stock organization.
Step 3: Handling efficiency
Examine picking routes, internal handling time and product accessibility. Dynamic storage systems should simplify these tasks.
Step 4: Safety
Consider operator and product safety. The chosen storage system must minimize the risk of accidents.
Step 5: Equipment compatibility
Check that the dynamic storage system is compatible with your existing handling equipment.
By following these steps and taking these criteria into account, you'll be able to choose the most suitable storage system, for a more efficient and profitable business.
Project Champagne Charpentier
Champagne Charpentier is a producer of champagne with low-temperature fermentation (36 months to 6 years maturation). They own 24 hectares of land and 9 cuvées.
- Customer project -
In Château-Thierry, Champagne Charpentier has created a new winemaking site. They therefore needed to equip the site's storeroom with a storage solution adapted to their voluminous production, the frequency of their product rotation and the preparation of their orders.
- The Provost solution -
In the same space, we created a specific high-density storage area with an electric shuttle and a picking area on dynamic frames (Carrier Pushback) perfectly adapted to their order preparation.
- 7 m high
- 15 pallets deep
- 405 pallets
High-density storage with shuttle to meet high demand at the end of the year.
Our high-density Last In - First Out storage system enables us to store bottles packed in palletized cartons, on 4 levels up to 7 meters high.
For better logistical stock management, this storage area is made up of 9 lanes corresponding to the number of vintages. Each lane can accommodate up to 15 pallets deep
The integration of a shuttle ensures the safety of forklift operators, who do not enter the storage aisles, and the integrity of the structure. One pallet is equivalent to 480 bottles, or 960 kg, and can represent a hazard when handled manually.
The available space is thus completely optimized, enabling storage of 405 pallets or 194,400 bottles (388 tons).