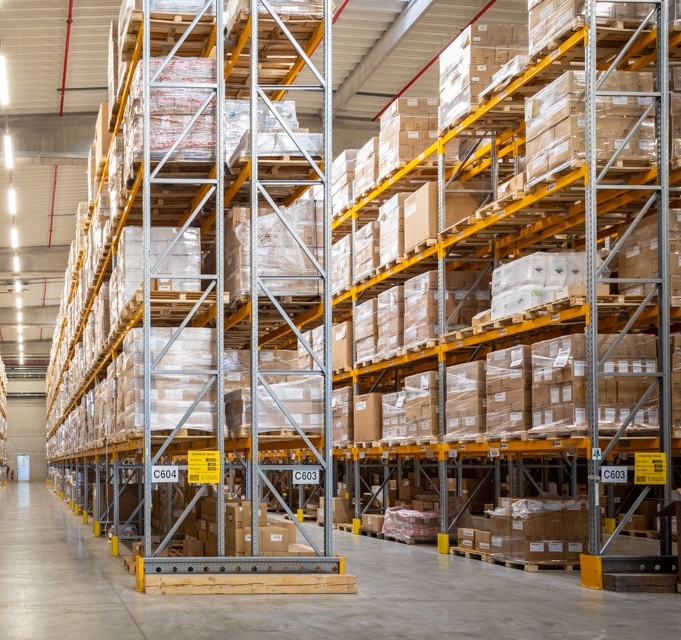
Methods for optimizing your storage
Provost, France's leading manufacturer of shelving and storage solutions, invites you to discover the main inventory management methods for efficiently organizing the storage of your items, raw materials and finished products in your logistics warehouses...
ABC method
The ABC (Activity Based Coasting) storage method is a technique for segmenting a company's various activities, in order to analyze costs and assess the profitability of each item. On the basis of this study, goods can be stored according to their turnover rate: the higher the rate, the closer the goods are to the operators and the easier they are to handle.
Principle of the ABC method:
- A: 80% of rotations and 20% of SKUs
- B: 15% of rotations and 30% of references
- C: 5% of rotations and 50% of references
Two versions are available:
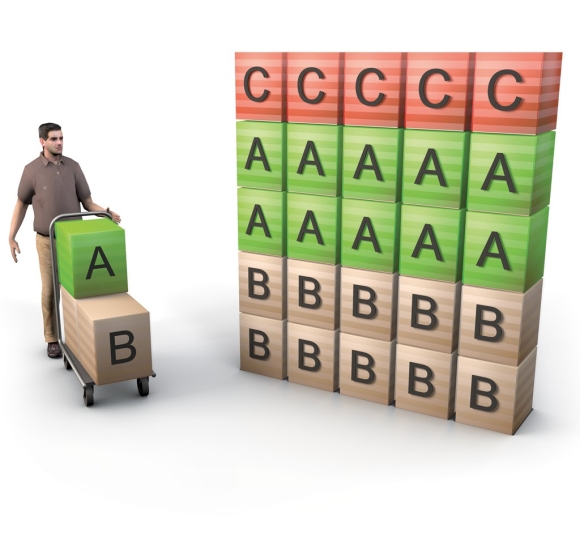
Storage with manual handling
In manual handling and picking storage, goods must be stored :
- A: at gripping height
- B: at the bottom of shelves
- C: high up
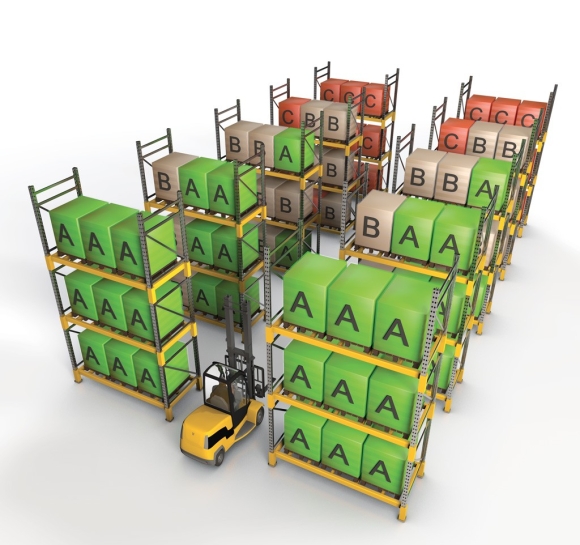
Warehouse storage
In the warehouse, goods must be stored :
- A: beginning of warehouse, close to goods-in and out
- B: middle of warehouse, close to goods in and out
- C: back of warehouse and aisles
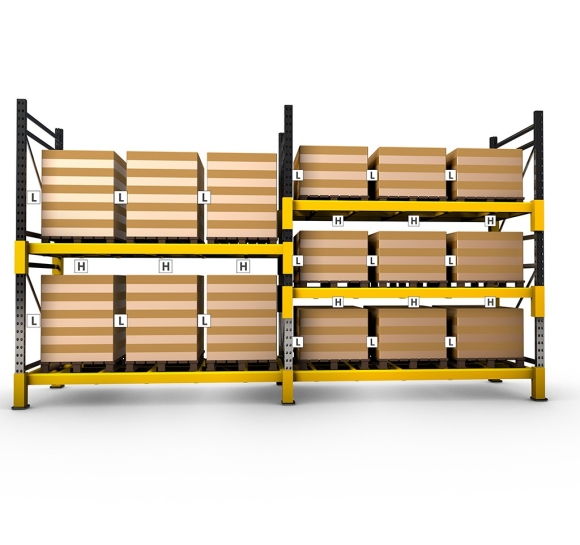
Inventory optimization
The aim of this method is to organize the available storage space in the best possible way, while leaving enough handling space for the operator or the forks of the forklift truck. It has a direct impact on the choice of storage equipment.
The handling clearance to be maintained will vary according to the type of product to be stored Archive storage :
- almost zero clearance to optimize storage
- Storage of light loads with manual handling: a lateral clearance (L) and a high clearance (H) of a few centimetres are sufficient to grip the goods
- Storage of heavy loads, pallets with handling equipment: a side clearance of 75mm (L) and a top clearance of 100mm (H) are recommended
LIFO - FIFO flow optimization
These two warehousing methods not only organize the flow of finished products or spare parts, but also enhance the value of inventories.
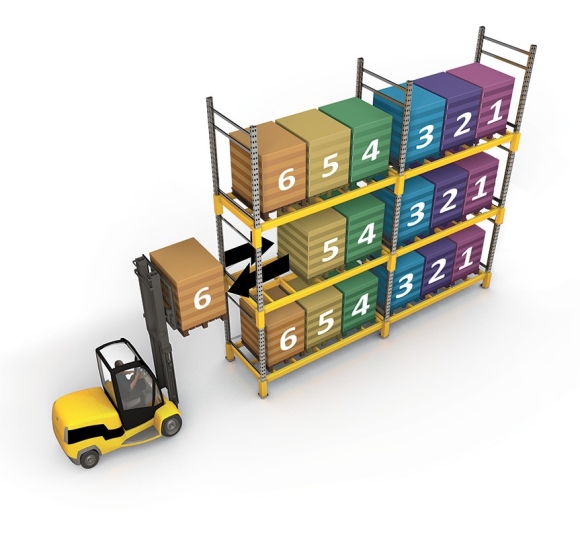
LIFO (Last In - First Out)
the last products to enter the warehouse are the first to leave, both physically and in terms of accounting. As the last deliveries are (depending on the storage system) often more quickly accessible, it is quicker for the operator to pick directly from the last arrivals. If the products handled by the company have no use-by date problems, this inventory management model can be consistent.
"Last in - first out": Single-access stacking/handling principle. This method will be used with accumulation storage
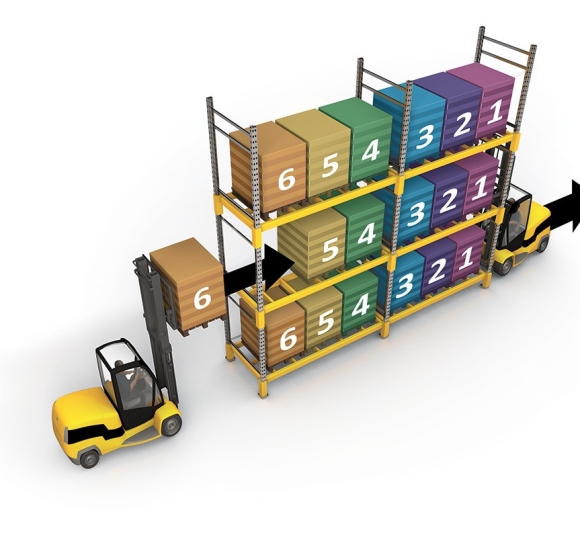
FIFO (First In - First Out)
the first products to enter the warehouse are the first to leave, both physically and in terms of accounting. This approach solves the problem of deterioration over time. This applies, for example, to perishable goods or product obsolescence.
"First-in-first-out" dynamic storage principle with double-access handling.
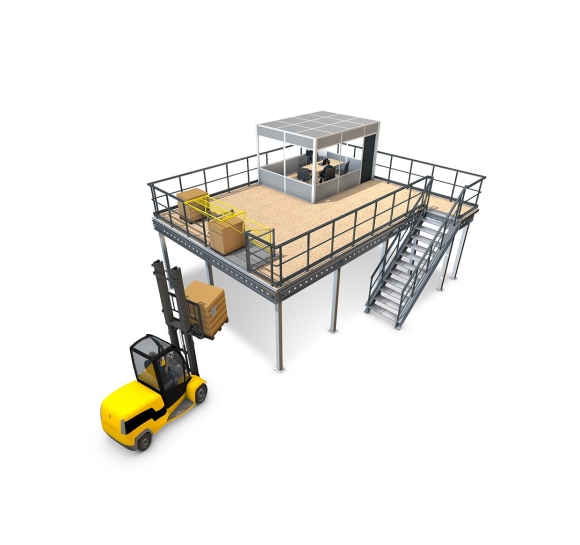
Methods and solutions for optimizing overhead storage
Mezzanine storage
Mezzanine storage platforms are extremely flexible in use and implementation, making it possible to optimize warehouse heights by doubling or tripling storage areas.
Combined with fixed storage elements or conveyors, industrial platforms can be used to increase stock density. This modular system easily adapts to changes in activity: expansion, changes in stock levels...
It can also be adapted to changes in a company, for example, by converting a storage area into offices.
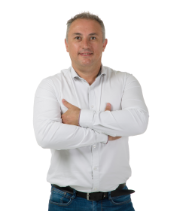
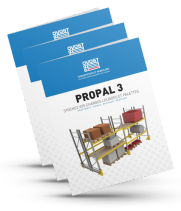